Series on the topics of fly ash concrete
The 5th topic: Assessment of Alkali Aggregate Reaction |
In 2007, the Concrete Committee of JSCE established a
subcommittee on design and application of fly ash
concrete to further promote the effective use of fly ash in accordance
with the performance-based design.
The subcommittee will report the activity of six working groups at
regular intervals in a newsletter in 2009. |
Fly ash helps prevent alkali aggregate reaction.
This advantage can be efficiently applied through the use of a guideline.
The committee investigated the influence of the quality of the fly ash,
the reactivity of the aggregate, and the condition of the alkali on the
fly ash’s ability to prevent alkali aggregate reaction. Mortar bar tests
showed that the JIS classification could be used to assess this ability.
This conclusion is supported by the strong relationship between the expansive
strain and the total surface area of amorphous silica. (Figure 1) The committee
also conducted concrete bar tests using several reactive aggregates, which
further confirmed the preventive effect of fly ash.
When concrete structures are electrochemically
desalinated to prevent reinforcement corrosion, the concrete’s alkali content
may become high, increasing the risk of an alkali aggregate reaction. Fly
ash reduces the degradation even when the alkali content is extremely high,
indicating that the preventive mechanism of fly ash works not only by reducing
the alkaline content but also by replacing the cement with fly ash.
As a result of the tests described above, the committee has proposed a replacement ratio for fly ash. Alkali aggregate reaction is caused by the reactivity of the aggregate, the reactive mineral content, and the alkaline content in the concrete. In some countries, several preventive measures are applied depending on the risk level, which is determined by the reactivity of the aggregate and the environmental conditions. However, this grading system is difficult to apply in Japan because the reactivity of the aggregate is unpredictable due to the complexity of Japan’s volcanic geological structure.
First, the committee classified the levels of countermeasures
as “normal” and “high.” Table 1 shows several theoretical cases and the
level of countermeasures to be applied. The “normal” level is for preventive
maintenance.
Second, based on tests and research, the committee
proposed the use of fly ash. Table 2 shows the recommended replacement
ratio for fly ash. The replacement ratio depends on the quality of the
fly ash and the level of countermeasures. The former is classified in accordance
with the Japan Industrial Standard (JIS A 6201). Note that the JIS does
not consider the CaO content. The fly ash currently produced in Japan rarely
contains more than 8% CaO. Therefore, the recommended replacement ratio
shown in Table 2 should be modified when fly ash with a high CaO content
is produced in the future.
Because the alkali aggregate reaction strongly
depends on the alkaline content of the concrete, the preventive measures
also depend on the alkaline content. When the risk is higher due to the
presence of foreign alkaline ions, the replacement ratio for fly ash should
be higher than the value shown in Table 2.
|
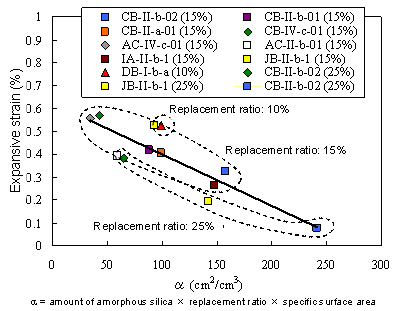
Figure 1 Relationship between expansive strain and surface area of amorphous
silica in fly ash
Table 1. Several theoretical cases and the level of countermeasure to be
applied
Theoretical Case |
Level of Countermeasure |
Highly reactive aggregate and highly reactive mineral content |
High level |
To ensure protection from ASR (e.g.,important structure) |
High level |
Difficult to predict aggregate reactivity and amount of and variation in reactive minerals |
High level |
Likely to contain little reactive aggregate |
Normal level |
Total alkaline content in concrete is higher than the regulatory value (3 kg/m3) |
Normal level |
|
Table 2. Recommended replacement ratio for fly ash to prevent ASR
Quality of fly ash |
Normal Level |
High Level |
JIS type II or more, JIS type IV (surface area: 2,500 cm2/g or more) |
15 % or more |
20 % or more |
Others |
30 % |
- |
|
|
|