RECYCLING CONCRETE WASTE MATERIALS USING COMPACTION
Biruktawit Taye Tarekegne1, Yuya Sakai2, and Toshiharu Kishi3
1 Graduate student, School of Engineering, The University of Tokyo, birktyg@iis.u-tokyo.ac.jp
2 Assistant professor, IIS, The University of Tokyo, ysakai@iis.u-tokyo.ac.jp
3 Professor, IIS, The University of Tokyo, kishi@iis.u-tokyo.ac.jp
ABSTRACT
Large amounts of waste concrete are produced in developed countries by disasters and the demolition of old structures. Currently, waste concrete is mainly recycled as a base course material for road construction. Developed countries, however, are expected to construct fewer roads in the future. Previous research has shown that a chemical bond forms in hardened cement paste powder upon compaction, resulting in mechanical performance that is similar to that of the original paste. This study examined the formation of these chemical bonds to determine if an alternative means could be developed for recycling old concrete. Experiments showed that the bond is more dependent on the size of concrete powder than on the original water to cement ratio.
1. INTRODUCTION
Concrete is the most common construction material and it can last a long time. However, it deteriorates over time for numerous reasons and needs regular maintenance and eventual replacement. This study investigated the utilization of concrete powder compaction as an alternative means of recycling concrete. Soroka and Sereda (1970) pointed out that solid-to-solid contact of surfaces resulting from the compaction of hydrated cement paste powder formed inter-particle bonds. Powder compression, on the other hand, has long been the dominant technique in the pharmaceutical industry for forming tablets and is equally essential for powder metallurgy and structural ceramics production.
2. EXPERIMENTAL APPROACH
Concrete samples were dried in a 400C chamber for 48 hours, manually reduced to a maximum particle size of 10 mm, and ground to a finer size using a mechanical-jaw crusher and a grinder.
The prepared powders were then pressed using the wet bag method in an isostatic pressing machine (Fig. 1(a)). This recycling method was selected because the pressure is applied uniformly to all of the outer surfaces of the forming mold, resulting in highly uniform consolidation. In this method, the concrete powder is poured into 1-cm cubic silicon molds and sealed airtight using plastic film (Fig. 1(b)). The sealed mold is then immersed for 3 minutes in a high-pressure vessel containing water as the compression medium.
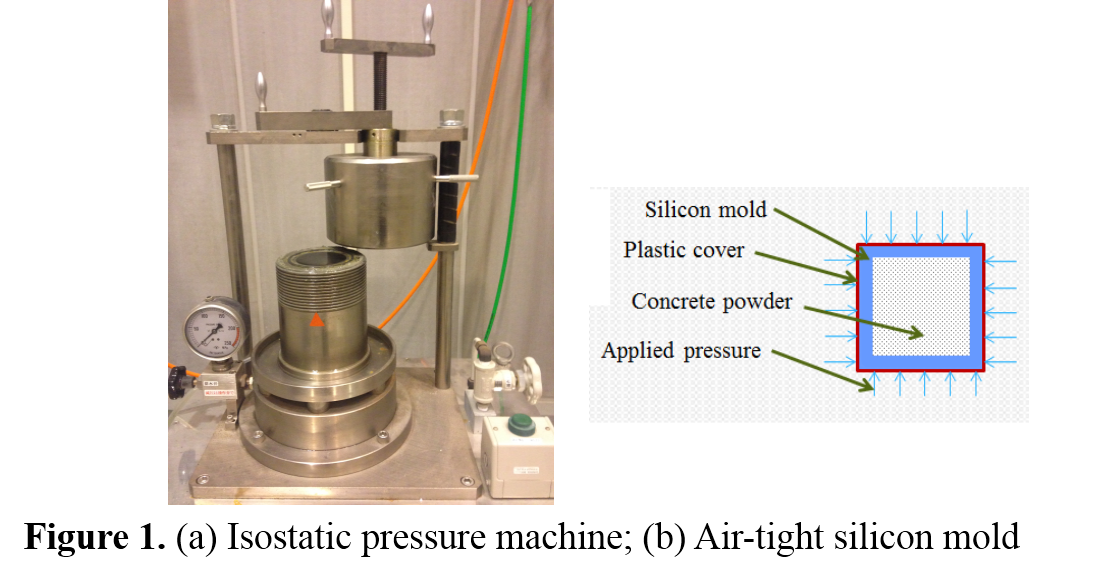
3. RESULT AND DISCUSSION
Figure 2 compares the average compressive strengths and the maximum concrete power particle sizes of concrete samples with three water-cement (w/c) ratios and compacted with a compression force of 200 MPa.
The compressive strength growth trends of the different water cement ratios were similar, rising more rapidly as the maximum particle size became smaller than 600 µm. As the maximum size of the concrete powder particles decreased from 1180 µm to 600 µm, the average strength of the compacted concrete samples with three different water-to-cement ratios increased by an average of 2 MPa. A further reduction in the maximum concrete powder particle size to 101.5 µm resulted in a relatively higher average compressive strength gain of 17 MPa. However, the average difference between the strengths of the 40% and the 70% w/c specimens of different particle sizes was only 4 MPa. The increased concrete strength of the finer powder particles is probably due to the increase in attainable interparticulate bond resulting from greater surface area.
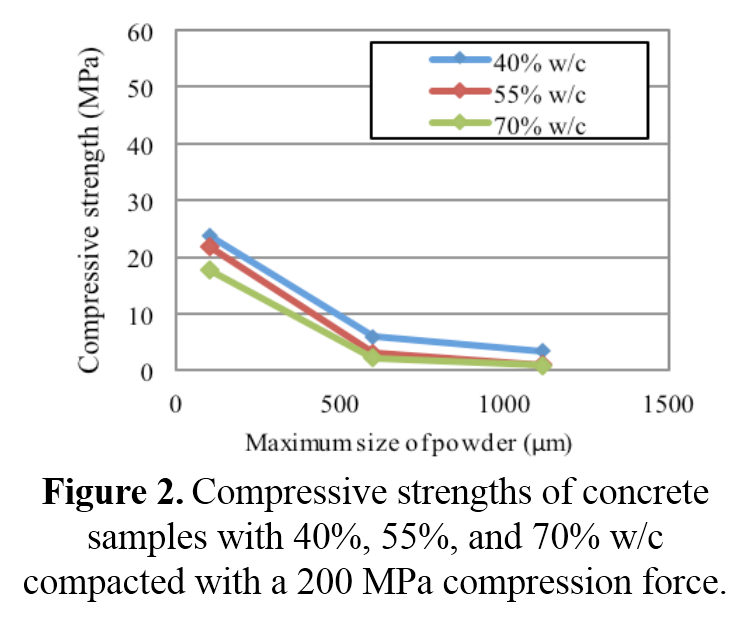
4. CONCLUSION
The compressive strength of the recycled concrete specimens prepared using powder compaction was significantly affected by the particle size of the concrete powder. The variation in the water cement ratio, however, had relatively little effect on the compressive strength.
REFERENCES
I. Soroka, P.J. Sereda. The structure of cement stone and the use of compacts as structural models. Proc. 5th Int. Symp. on the Chemistry of Cement, Tokyo (1968), pp. 67–73 Part III
|